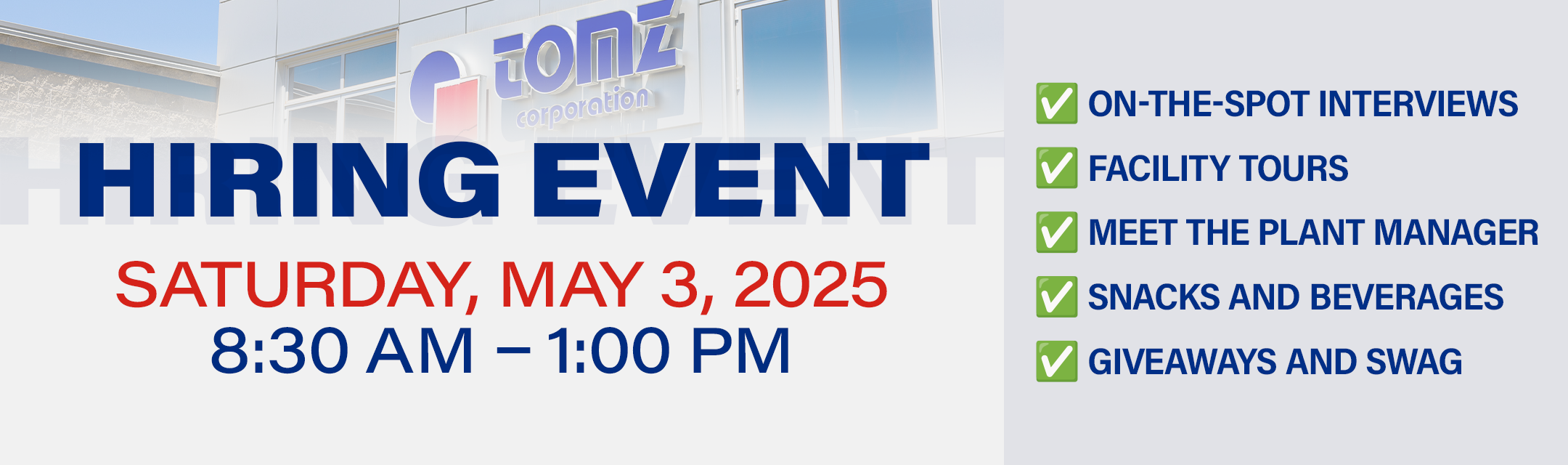
Summary of Position
Reporting to the Operations Supervisor, this position will have direct responsibility for the set-up and manufacture of components within the Swiss machining department. TOMZ manufactures parts via high- precision metal machining, finishing, assembly, and anodizing processes for Medical Devices. The successful candidate will be expected to maintain the ISO 13485 standards documentation, set up and operate equipment, and perform visual and dimensional inspections on machined components using various precision measuring equipment.
Essential Functions
- Operate and maintain Citizen Lathes, Tsugami Lathes, Index multi-spindle lathes, 3-4-5 axis production equipment, including Robo Drills, Mill Turn, and horizontal/vertical mills.
- Perform offsets and tool changes to ensure efficient production with minimal support.
- Set up complex legacy components and new production orders for steady machine operation.
- Conduct visual and dimensional inspections using microscopes, micrometers, calipers, pin gauges, thread gauges, comparators, Micro-Hite, CMM, and vision systems.
- Perform scheduled and regular preventive maintenance on equipment.
- Drive problem-solving activities for complex machine or process issues.
- Complete and compile documentation related to quality inspection standards.
- Ensure proper material control, identification, and traceability for conforming and nonconforming materials.
- Support Quality Best Practices and contribute to continuous improvement in GDP/GMP.
- Capable of mentoring and training lower-level machinists.
- Facilitate a continuous improvement in culture and ensure quality and delivery objectives are met.
- Utilize ERP and QMS systems to document and control inspection and traceability activities.
- Maintain safe working conditions and follow occupational safety and health requirements, including PPE guidance.
- Adhere to the TOMZ Quality Management System.
- Perform other duties as assigned.
Qualifications:
Education
- Certification from a technical school program or equivalent, directly transferable work experience in a manufacturing or engineering discipline may be accepted.
- Certification from a technical school program is strongly preferred.
Experience
- Minimum of 3-7 years’ experience in a regulated manufacturing environment.
Qualifications
- Experience in Class I, II, and/or III medical device manufacturing within a regulated environment using calibrated equipment and hazardous materials.
- Relevant job experience in regulated manufacturing, with industry experience in aerospace, defense, or automotive.
- Knowledge of and experience with GMP/ISO standards.
- A self-starter capable of working independently and as part of a team, with the ability to collaborate across various functional areas, including R&D, Manufacturing, and QA, to achieve results with minimal guidance.
- Advanced understanding of mechanical equipment usage, care, and inspection processes.
- Ability to use hand-held tools for preventive maintenance, repairs, and tool changes.
- Skilled in reading and understanding of blueprints, specifications, and procedures.
- Detail-oriented with the ability to maintain accuracy and complete tasks promptly.
- Proficient in identifying nonconformances and maintaining organization.
- Intermediate skills in GD&T.
Preferred Skills
- Strong verbal and written English language communication skills.
Physical Demands
- Ability to bend, stoop, squat, kneel, and lift up to 50 pounds. Team lift or mechanical assistance required for objects over 50 pounds.
- Perform repetitive hand and arm movements while lifting up to 20 pounds, including gripping, twisting, and placing components for extended periods, and lifting objects overhead.
- 20/20 vision (assisted or unassisted) required for sorting raw and non-conforming materials. Good dexterity is needed for managing small to medium products.
- Exposure to oil, grease, occupational noise, cleaning solvents, dust, metal particles, sparks, coolant, and sharp-edged materials. Personal protective equipment (PPE) such as safety glasses, dust masks, ear plugs, cut-resistant or chemical-resistant gloves, and engineering controls may be required.
- Ability to sit or stand for prolonged periods.
WEEKEND SHIFT: 20% DIFFERENTIAL 5AM-5PM FRI-SUN
2ND SHIFT: 15% DIFFERENTIAL 5PM-3:30AM
Job Features
Summary of Position Reporting to the Operations Supervisor, this position will have direct responsibility for the set-up and manufacture of components within the Swiss machining department. TOMZ manuf...
Summary of Position
Reporting to the Operations Supervisor, this position will have direct responsibility for the manufacturing of components through various basic functions within the Department. TOMZ manufactures parts via high precision metal machining, finishing, assembly, and anodizing processes for Medical Devices. The successful candidate will be expected to maintain the ISO 13485 standards documentation, operate equipment, and perform visual and dimensional inspections on machine components.
Essential Functions
- Operate and maintain 3-4-5 axis production equipment, including Robo Drills, Mill Turn, and horizontal/vertical mills. Citizen Lathes, Tsugami Lathes, Index multi-spindle lathes.
- Perform visual and dimensional inspections on manufactured components, as required using a microscope, micrometer, caliper, pin gauges, thread gauges, comparator, Micro-Hite, etc.
- Support problem-solving activities for complex machine or process issues.
- Complete and compile documentation related to quality inspection standards.
- Ensure proper material control, identification, and traceability for conforming and nonconforming materials.
- Support Quality Best Practices and contribute to continuous improvement efforts of GDP/GMP.
- Utilize ERP and QMS systems to document and control inspection and traceability activities.
- Must maintain safe working conditions and follow occupational safety and health requirements including Personal Protective Equipment (PPE) guidance and rules.
- Adhere to the TOMZ Quality Management System.
- Perform other duties as assigned.
Qualifications:
Experience
- Minimum of 0-2 years’ experience in a regulated manufacturing environment.
Qualifications
- Basic understanding of the usage and care of mechanical equipment and inspection processes.
- Ability to use hand-held tools for preventive maintenance, repairs, and tool changes.
- Ability to effectively read and understand blueprints, specifications, and procedures.
- Detail-oriented with the ability to maintain accuracy and complete tasks promptly.
- Basic understanding of GD&T.
- Knowledge of GMP/ISO standards.
Preferred Skills
- Class I, II and/or III Medical Device manufacturing experience.
- Regulated manufacturing industry experience (e.g., aerospace, defense, pharmaceutical, etc.)
- Strong verbal and written English language communication skills.
Physical Demands
- Ability to bend, stoop, squat, kneel, and lift up to 50 pounds. Team lift or mechanical assistance required for objects over 50 pounds.
- Perform repetitive hand and arm movements while lifting up to 20 pounds, including gripping, twisting, and placing components for extended periods, and lifting objects overhead.
- 20/20 vision (assisted or unassisted) required for sorting raw and non-conforming materials. Good dexterity is needed for managing small to medium products.
- Exposure to oil, grease, occupational noise, cleaning solvents, dust, metal particles, sparks, coolant, and sharp-edged materials. Personal protective equipment (PPE) such as safety glasses, dust masks, ear plugs, cut-resistant or chemical-resistant gloves, and engineering controls may be required.
- Ability to sit or stand for prolonged periods.
Job Features
Summary of Position Reporting to the Operations Supervisor, this position will have direct responsibility for the manufacturing of components through various basic functions within the Department. TOM...
TOMZ Corporation, a growing leader in manufacturing of devices and components for major medical device companies, is looking for a motivated CNC Machinist to join our organization. TOMZ offers competitive compensation and excellent benefits, including 401k, health/dental, vision, and paid time off. TOMZ maintains a modern, clean, and safe facility with state-of-the-art equipment and dedication to continuous process improvement. TOMZ is registered with the FDA as a Class 2 and Class 3 Medical Device Manufacturer and certified to ISO 13485.
Summary of Position
Reporting to the Operations Supervisor, this position will have direct responsibility for the set-up and manufacture of components within the Swiss machining department. TOMZ manufactures parts via high- precision metal machining, finishing, assembly, and anodizing processes for Medical Devices. The successful candidate will be expected to maintain the ISO 13485 standards documentation, set up and operate equipment, and perform visual and dimensional inspections on machined components using various precision measuring equipment.
Essential Functions
- Set up and operate and maintain Citizen Lathes or Tsugami Lathes.
- Perform offsets and tool changes to ensure efficient production with minimal support.
- Set up complex legacy components and new production orders for steady machine operation.
- Perform preventative maintenance on Swiss Lathe to ensure consistent machine performance
- Conduct visual and dimensional inspections using microscopes, micrometers, calipers, pin gauges, thread gauges, comparators, Micro-Hite, CMM, and vision systems.
- Perform scheduled and regular preventive maintenance on equipment.
- Drive problem-solving activities for complex machine or process issues.
- Complete and compile documentation related to quality inspection standards.
- Ensure proper material control, identification, and traceability for conforming and nonconforming materials.
- Support Quality Best Practices and contribute to continuous improvement in GDP/GMP.
- Capable of mentoring and training lower-level machinists.
- Facilitate a continuous improvement in culture and ensure quality and delivery objectives are met.
- Utilize ERP and QMS systems to document and control inspection and traceability activities.
- Maintain safe working conditions and follow occupational safety and health requirements, including PPE guidance.
- Adhere to the TOMZ Quality Management System.
- Perform other duties as assigned.
Qualifications:
Education
- Certification from a technical school program or equivalent, directly transferable work experience in a manufacturing or engineering discipline may be accepted.
- Certification from a technical school program is strongly preferred.
Experience
- Minimum of 3-7 years’ experience in a regulated manufacturing environment.
Qualifications
- Experience in Class I, II, and/or III medical device manufacturing within a regulated environment using calibrated equipment and hazardous materials.
- Strong math background, preferable in machine math/shop math
- Relevant job experience in regulated manufacturing, with industry experience in aerospace, defense, or automotive.
- Knowledge of and experience with GMP/ISO standards.
- A self-starter capable of working independently and as part of a team, with the ability to collaborate across various functional areas, including R&D, Manufacturing, and QA, to achieve results with minimal guidance.
- Advanced understanding of mechanical equipment usage, care, and inspection processes.
- Ability to use hand-held tools for preventive maintenance, repairs, and tool changes.
- Skilled in reading and understanding of blueprints, specifications, and procedures.
- Detail-oriented with the ability to maintain accuracy and complete tasks promptly.
- Proficient in identifying nonconformances and maintaining organization.
- Intermediate skills in GD&T.
Preferred Skills
- Strong verbal and written English language communication skills.
Physical Demands
- Ability to bend, stoop, squat, kneel, and lift up to 50 pounds. Team lift or mechanical assistance required for objects over 50 pounds.
- Perform repetitive hand and arm movements while lifting up to 20 pounds, including gripping, twisting, and placing components for extended periods, and lifting objects overhead.
- 20/20 vision (assisted or unassisted) required for sorting raw and non-conforming materials. Good dexterity is needed for managing small to medium products.
- Exposure to oil, grease, occupational noise, cleaning solvents, dust, metal particles, sparks, coolant, and sharp-edged materials. Personal protective equipment (PPE) such as safety glasses, dust masks, ear plugs, cut-resistant or chemical-resistant gloves, and engineering controls may be required.
- Ability to sit or stand for prolonged periods.
Job Features
TOMZ Corporation, a growing leader in manufacturing of devices and components for major medical device companies, is looking for a motivated CNC Machinist to join our organization. TOMZ offers competi...
TOMZ Corporation, a leader in manufacturing of devices and components for major medical device companies, is looking for a motivated CNC Machinist to join our organization. TOMZ offers competitive compensation and excellent benefits, including 401k, health/dental, vision, and paid time off. TOMZ maintains a modern, clean, and safe facility with state-of-the-art equipment and dedication to continuous process improvement. TOMZ is registered with the FDA as a Class 2 and Class 3 Medical Device Manufacturer and certified to ISO 13485.
Summary of Position
Reporting to the Operations Supervisor, this position will have direct responsibility for the set-up and manufacture of components within a machining Department. TOMZ manufactures parts via high- precision metal machining, finishing, assembly, and anodizing processes for Medical Devices. The successful candidate will be expected to maintain the ISO 13485 standards documentation, set up and operate equipment, and perform visual and dimensional inspections on machined components using various precision measuring equipment.
Essential Functions
- Set up and operate and maintain Citizen Lathes or Tsugami Lathes
- Perform offsets and tool changes to ensure efficient production with minimal support.
- Set up legacy components and new production orders for steady machine operation.
- Perform preventative maintenance on Swiss Lathe to ensure consistent machine performance
- Conduct visual and dimensional inspections using microscopes, micrometers, calipers, pin gauges, thread gauges, comparators, Micro-Hite, CMM, and vision systems.
- Perform scheduled and regular preventive maintenance on equipment.
- Drive problem-solving activities for complex machine or process issues.
- Complete and compile documentation related to quality inspection standards.
- Ensure proper material control, identification, and traceability for conforming and nonconforming materials.
- Support Quality Best Practices and contribute to continuous improvement in GDP/GMP.
- Utilize ERP and QMS systems to document and control inspection and traceability activities.
- Maintain safe working conditions and follow occupational safety and health requirements, including PPE guidance.
- Adhere to the TOMZ Quality Management System.
- Perform other duties as assigned.
Qualifications:
Education
- High school diploma, GED, or equivalent directly transferrable work experience (Manufacturing or Engineering discipline preferred).
- Certification from a technical school program preferred.
Experience
- Minimum of 2-5 years’ experience in a regulated manufacturing environment.
Qualifications
- Experience in Class I, II, and/or III medical device manufacturing within a regulated environment using calibrated equipment and hazardous materials.
- Strong math background, preferable in machine math/shop math
- Relevant job experience in regulated manufacturing, with industry experience in aerospace, defense, or automotive.
- Knowledge of and experience with GMP/ISO standards.
- A self-starter capable of working independently and as part of a team, with the ability to collaborate across various functional areas, including R&D, Manufacturing, and QA, to achieve results with guidance.
- Understanding of mechanical equipment usage, care, and inspection processes.
- Ability to use hand-held tools for preventive maintenance, repairs, and tool changes.
- Effectively read and understand blueprints, specifications and procedures.
- Understanding of GD&T.
- Detail-oriented with the ability to maintain accuracy and complete tasks promptly.
- Identify nonconformances and maintain organization.
Preferred Skills
- Strong verbal and written English language communication skills.
Physical Demands
- Ability to bend, stoop, squat, kneel, and lift up to 50 pounds. Team lift or mechanical assistance required for objects over 50 pounds.
- Perform repetitive hand and arm movements while lifting up to 20 pounds, including gripping, twisting, and placing components for extended periods, and lifting objects overhead.
- 20/20 vision (assisted or unassisted) required for sorting raw and non-conforming materials. Good dexterity is needed for managing small to medium products.
- Exposure to oil, grease, occupational noise, cleaning solvents, dust, metal particles, sparks, coolant, and sharp-edged materials. Personal protective equipment (PPE) such as safety glasses, dust masks, ear plugs, cut-resistant or chemical-resistant gloves, and engineering controls may be required.
- Ability to sit or stand for prolonged periods
Job Features
TOMZ Corporation, a leader in manufacturing of devices and components for major medical device companies, is looking for a motivated CNC Machinist to join our organization. TOMZ offers competitive com...
TOMZ Corporation, a leader in manufacturing of devices and components for major medical device companies, is looking for a motivated CNC Machinist to join our organization. TOMZ offers competitive compensation and excellent benefits, including 401k, health/dental, vision, and paid time off. TOMZ maintains a modern, clean, and safe facility with state-of-the-art equipment and dedication to continuous process improvement. TOMZ is registered with the FDA as a Class 2 and Class 3 Medical Device Manufacturer and certified to ISO 13485. Growing manufacturer with new equipment!
Summary of Position
Reporting to the Operations Supervisor, this position will have direct responsibility for the set-up and manufacture of components within the Swiss machining department. TOMZ manufactures parts via high- precision metal machining, finishing, assembly, and anodizing processes for Medical Devices. The successful candidate will be expected to maintain the ISO 13485 standards documentation, set up and operate equipment, and perform visual and dimensional inspections on machined components using various precision measuring equipment.
Essential Functions
- Set up and operate and maintain INDEX multi-spindle lathes.
- Perform offsets and tool changes to ensure efficient production with minimal support.
- Set up complex legacy components and new production orders for steady machine operation.
- Perform preventative maintenance on INDEX to ensure consistent machine performance
- Conduct visual and dimensional inspections using microscopes, micrometers, calipers, pin gauges, thread gauges, comparators, Micro-Hite, CMM, and vision systems.
- Perform scheduled and regular preventive maintenance on equipment.
- Drive problem-solving activities for complex machine or process issues.
- Complete and compile documentation related to quality inspection standards.
- Ensure proper material control, identification, and traceability for conforming and nonconforming materials.
- Support Quality Best Practices and contribute to continuous improvement in GDP/GMP.
- Capable of mentoring and training lower-level machinists.
- Facilitate a continuous improvement in culture and ensure quality and delivery objectives are met.
- Utilize ERP and QMS systems to document and control inspection and traceability activities.
- Maintain safe working conditions and follow occupational safety and health requirements, including PPE guidance.
- Adhere to the TOMZ Quality Management System.
- Perform other duties as assigned.
Qualifications:
Education
- Certification from a technical school program or equivalent, directly transferable work experience in a manufacturing or engineering discipline may be accepted.
- Certification from a technical school program is strongly preferred.
Experience
- Minimum of 3-7 years’ experience in a regulated manufacturing environment.
Qualifications
- Experience in Class I, II, and/or III medical device manufacturing within a regulated environment using calibrated equipment and hazardous materials.
- Strong math background, preferable in machine math/shop math
- Relevant job experience in regulated manufacturing, with industry experience in aerospace, defense, or automotive.
- Knowledge of and experience with GMP/ISO standards.
- A self-starter capable of working independently and as part of a team, with the ability to collaborate across various functional areas, including R&D, Manufacturing, and QA, to achieve results with minimal guidance.
- Advanced understanding of mechanical equipment usage, care, and inspection processes.
- Ability to use hand-held tools for preventive maintenance, repairs, and tool changes.
- Skilled in reading and understanding of blueprints, specifications, and procedures.
- Detail-oriented with the ability to maintain accuracy and complete tasks promptly.
- Proficient in identifying nonconformances and maintaining organization.
- Intermediate skills in GD&T.
Preferred Skills
- Strong verbal and written English language communication skills.
Physical Demands
- Ability to bend, stoop, squat, kneel, and lift up to 50 pounds. Team lift or mechanical assistance required for objects over 50 pounds.
- Perform repetitive hand and arm movements while lifting up to 20 pounds, including gripping, twisting, and placing components for extended periods, and lifting objects overhead.
- 20/20 vision (assisted or unassisted) required for sorting raw and non-conforming materials. Good dexterity is needed for managing small to medium products.
- Exposure to oil, grease, occupational noise, cleaning solvents, dust, metal particles, sparks, coolant, and sharp-edged materials. Personal protective equipment (PPE) such as safety glasses, dust masks, ear plugs, cut-resistant or chemical-resistant gloves, and engineering controls may be required.
- Ability to sit or stand for prolonged periods.
Job Features
TOMZ Corporation, a leader in manufacturing of devices and components for major medical device companies, is looking for a motivated CNC Machinist to join our organization. TOMZ offers competitive com...
TOMZ Corporation, a leader in manufacturing of devices and components for major medical device companies, is looking for a motivated CNC Machinist to join our organization. TOMZ offers competitive compensation and excellent benefits, including 401k, health/dental, vision, and paid time off. TOMZ maintains a modern, clean, and safe facility with state-of-the-art equipment and dedication to continuous process improvement. TOMZ is registered with the FDA as a Class 2 and Class 3 Medical Device Manufacturer and certified to ISO 13485. TOMZ has won new business and is growing! Looking for new talent to bring on!
Summary of Position
Reporting to the Operations Supervisor, this position will have direct responsibility for the set-up and manufacture of components within a machining Department. TOMZ manufactures parts via high- precision metal machining, finishing, assembly, and anodizing processes for Medical Devices. The successful candidate will be expected to maintain the ISO 13485 standards documentation, set up and operate equipment, and perform visual and dimensional inspections on machined components using various precision measuring equipment.
Essential Functions
- Set up, operate and maintain INDEX multi-spindle lathes.
- Perform offsets and tool changes to ensure efficient production with minimal support.
- Set up legacy components and new production orders for steady machine operation.
- Perform preventative maintenance on INDEX machine to ensure consistent machine performance
- Conduct visual and dimensional inspections using microscopes, micrometers, calipers, pin gauges, thread gauges, comparators, Micro-Hite, CMM, and vision systems.
- Perform scheduled and regular preventive maintenance on equipment.
- Drive problem-solving activities for complex machine or process issues.
- Complete and compile documentation related to quality inspection standards.
- Ensure proper material control, identification, and traceability for conforming and nonconforming materials.
- Support Quality Best Practices and contribute to continuous improvement in GDP/GMP.
- Utilize ERP and QMS systems to document and control inspection and traceability activities.
- Maintain safe working conditions and follow occupational safety and health requirements, including PPE guidance.
- Adhere to the TOMZ Quality Management System.
- Perform other duties as assigned.
Qualifications:
Education
- High school diploma, GED, or equivalent directly transferrable work experience (Manufacturing or Engineering discipline preferred).
- Certification from a technical school program preferred.
Experience
- Minimum of 2-5 years’ experience in a regulated manufacturing environment.
Qualifications
- Experience in Class I, II, and/or III medical device manufacturing within a regulated environment using calibrated equipment and hazardous materials.
- Strong math background, preferable in machine math/shop math
- Relevant job experience in regulated manufacturing, with industry experience in aerospace, defense, or automotive.
- Knowledge of and experience with GMP/ISO standards.
- A self-starter capable of working independently and as part of a team, with the ability to collaborate across various functional areas, including R&D, Manufacturing, and QA, to achieve results with guidance.
- Understanding of mechanical equipment usage, care, and inspection processes.
- Ability to use hand-held tools for preventive maintenance, repairs, and tool changes.
- Effectively read and understand blueprints, specifications and procedures.
- Understanding of GD&T.
- Detail-oriented with the ability to maintain accuracy and complete tasks promptly.
- Identify nonconformances and maintain organization.
Preferred Skills
- Strong verbal and written English language communication skills.
Physical Demands
- Ability to bend, stoop, squat, kneel, and lift up to 50 pounds. Team lift or mechanical assistance required for objects over 50 pounds.
- Perform repetitive hand and arm movements while lifting up to 20 pounds, including gripping, twisting, and placing components for extended periods, and lifting objects overhead.
- 20/20 vision (assisted or unassisted) required for sorting raw and non-conforming materials. Good dexterity is needed for managing small to medium products.
- Exposure to oil, grease, occupational noise, cleaning solvents, dust, metal particles, sparks, coolant, and sharp-edged materials. Personal protective equipment (PPE) such as safety glasses, dust masks, ear plugs, cut-resistant or chemical-resistant gloves, and engineering controls may be required.
- Ability to sit or stand for prolonged periods
Job Features
TOMZ Corporation, a leader in manufacturing of devices and components for major medical device companies, is looking for a motivated CNC Machinist to join our organization. TOMZ offers competitive com...
TOMZ Corporation is in search of a Quality Inspector to join our team! A leader in manufacturing of devices and components for major medical device companies, TOMZ offers competitive compensation and excellent benefits. Some of those include 401k, health/dental, vision and paid time off. TOMZ maintains a modern, clean, and safe facility with state-of-the-art equipment and dedication to continuous process improvement. TOMZ is registered with the FDA as a Class 2 and Class 3 Medical Device Manufacturer and is certified to ISO 13485.
Summary of Position
Reporting to the Department Manager, this position will have direct responsibility for the quality control functions within the Department. TOMZ manufactures parts via high precision metal machining, assembly, and anodize processes for Medical Devices. The successful candidate will be expected to maintain the ISO 13485 standards documentation and/or perform inspections on machined components · Perform further complex inspections on machined components utilizing methods such as comparators, CMM and/or various manual and automated techniques. Faced paced work environment.
Essential Functions
- Perform and provide training assistance for inspections on machined components, as required, utilizing conventional visual and layout inspection techniques and equipment. Ex. include microscopes, calipers, micrometers and gages.
- Execute Incoming, First Piece, FAI, In-process, and Final Inspection, as assigned.
- Completes and compiles necessary documentation related to Quality Inspection standards.
- Ensure proper material control, identification and traceability is maintained for conforming and nonconforming material through the manufacturing processes.
- Accurately review and ensure Good Document Practices (GDP) are upheld for Routers/Inspection Plans/Device History Records (DHRs) throughout the manufacturing process and in preparation for final lot release/shipment.
- Support Quality Best Practices and GDP/GMP continuous improvement efforts.
- Utilize and navigate ERP and QMS systems to ensure inspection and traceability activities are properly documented and controlled, as needed.
- Utilize the ERP system to prioritize and support product final acceptance and shipment, as needed.
- Generate Packing Slips and Certificates of Compliance (C of C) in accordance with TOMZ and/or customer requirements.
- Support physical and/or electronic record retention.
- Must follow occupational Safety and Health requirements including Personal Protective Equipment (PPE) guidance and rules.
- Adhere to the TOMZ Quality Management System.
- Perform other duties as assigned.
Qualifications:
Education
- High school diploma, GED, or equivalent directly transferrable work experience (Manufacturing or Engineering discipline preferred).
Experience
- Minimum of 3-5 years’ experience in a regulated manufacturing environment.
Qualifications
- Regulated manufacturing industry experience (e.g. Aerospace, Defense, Pharmaceutical, etc.)
- Ability to effectively read and understand blueprints, specifications, and procedures.
- Knowledge of dimensional, visual and mechanical inspection processes.
- Strong background concerning the usage and care of mechanical measurement equipment, tools and hand-held tools including micrometers, calipers, dial indicators, height gages, pin gages, etc.
- Maintains accuracy and attention to detail at all times and completes tasks in a timely manner.
- “Hands-on” self-starter with ability to work both independently and as part of a team.
- Strong verbal and written English language communication skills.
- Competency with Microsoft Office (i.e. Outlook, Word, Excel, and PowerPoint).
- Ability to work with a variety of functional areas, including R&D, Manufacturing, and QA, as required, accomplishing results with minimal guidance.
Preferred Skills
- Quality certification(s) (e.g. ASQ CQT, QCI, etc.).
- Class I, II and/or III Medical Device manufacturing experience.
- Knowledge of and experience with GMP/ISO standards.
TOMZ Corporation is in search of a Quality Inspector to join our team! A leader in manufacturing of devices and components for major medical device companies, TOMZ offers competitive compensation and ...
Our Mission
To enhance the lives of patients by sustainably manufacturing innovative medical devices for leading OEMs around the globe.
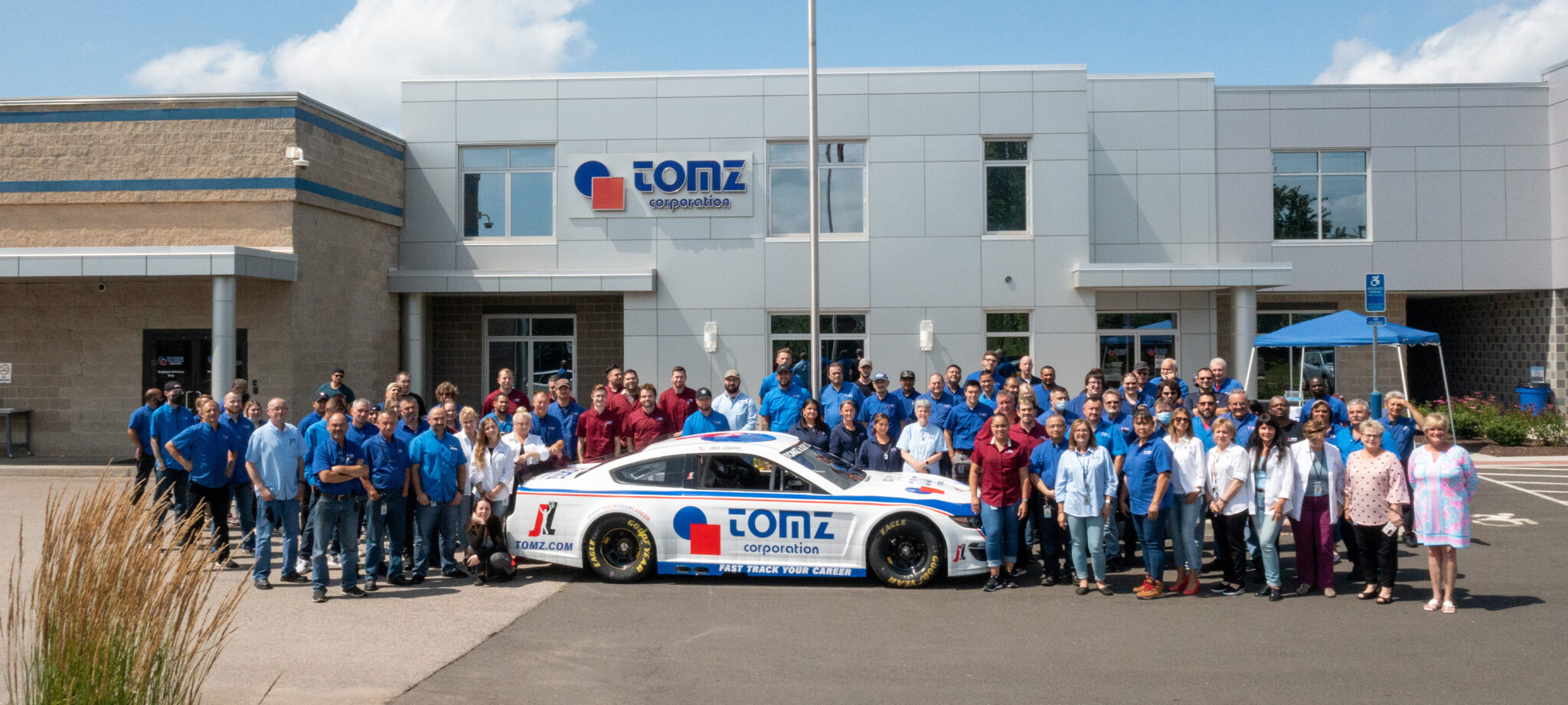
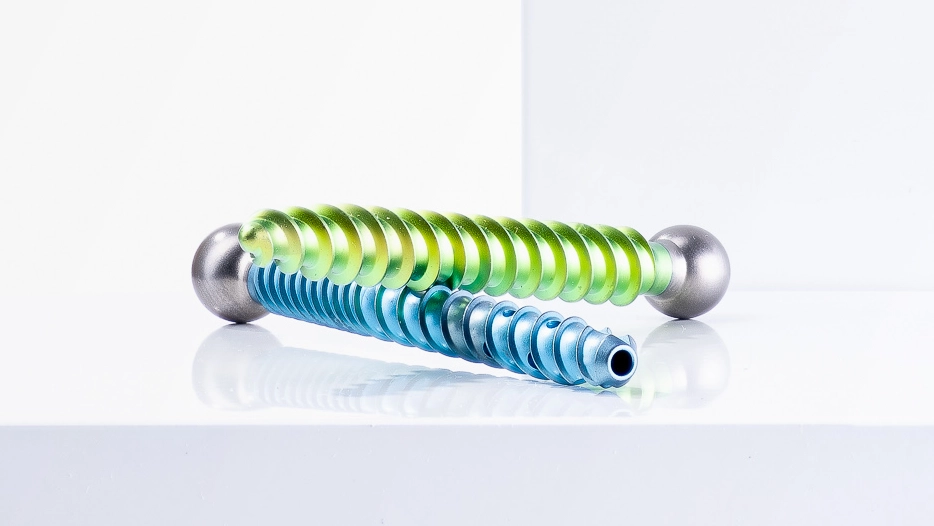
We Manufacture Medical Devices
We specialize in manufacturing the best medical device implants for medical teams and surgeons around the world. Most of our team will tell you that the work is very fulfilling because we help people live better lives.
Company Values & Culture
Our DNA is as unique as everyone that works here.
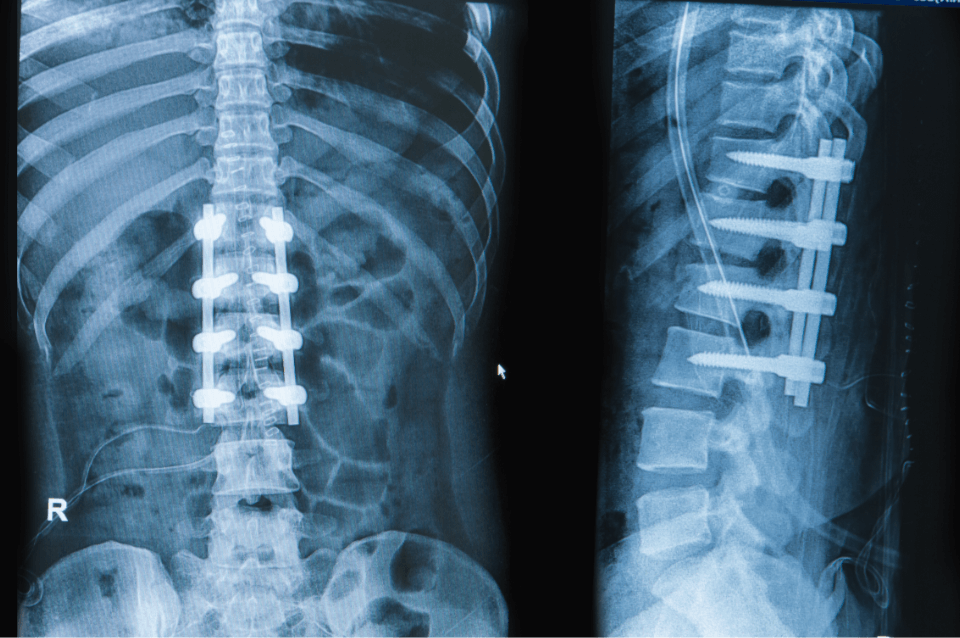
Put Patients First
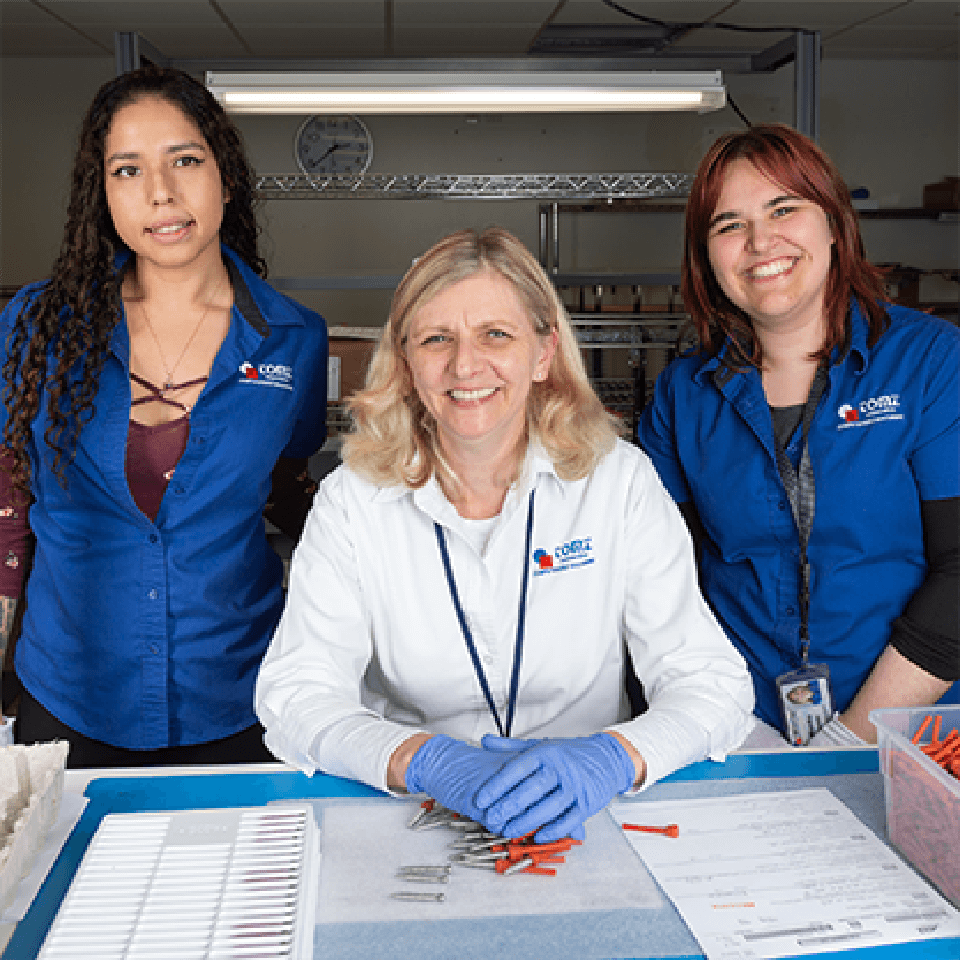
Embrace Diversity
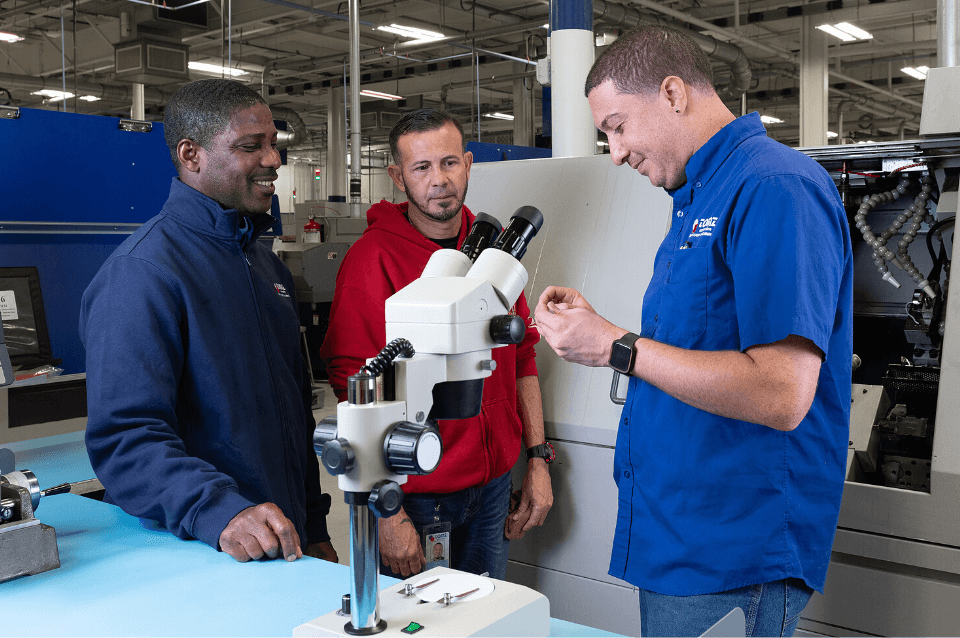
Learn & Grow
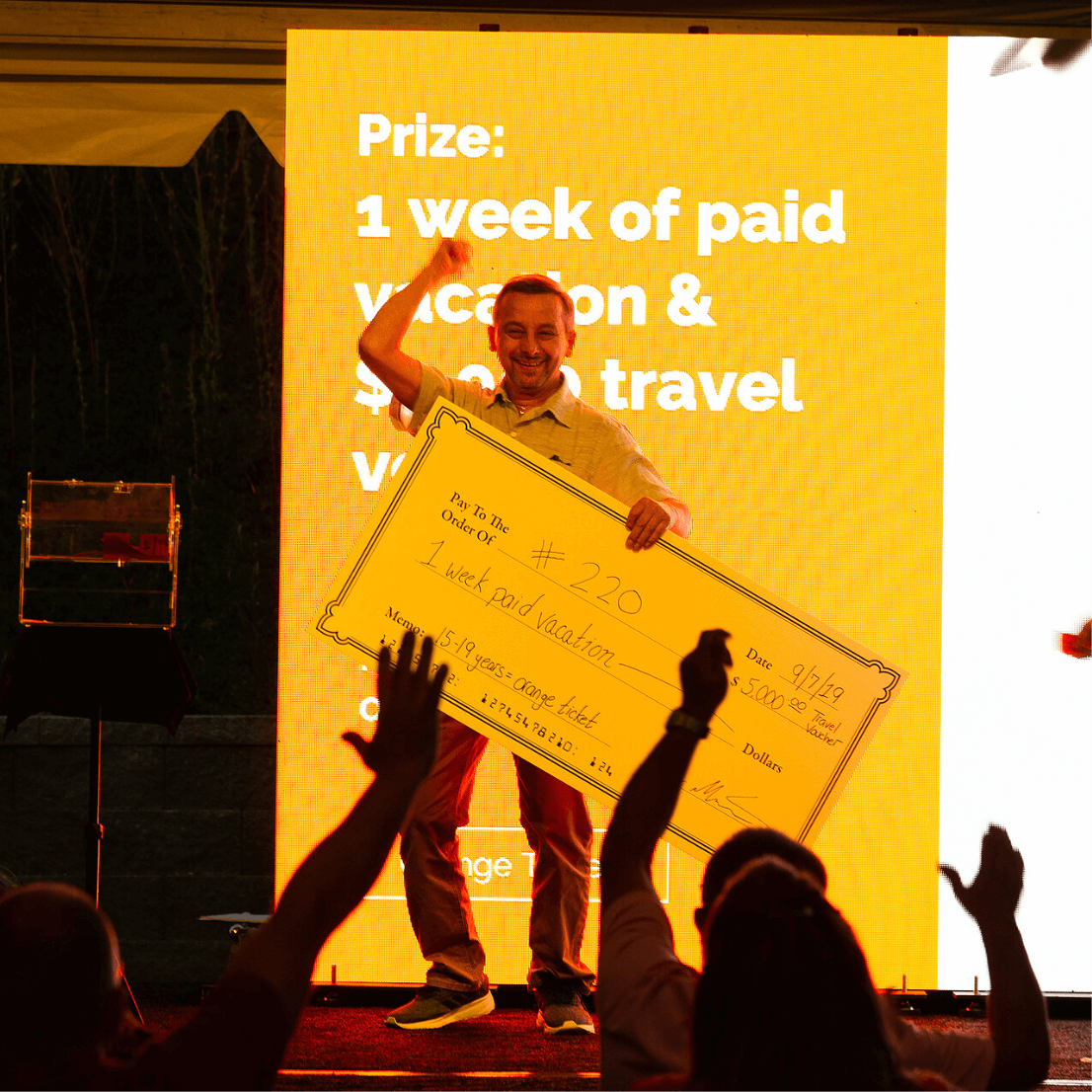
Reward Great Effort
Why Work at TOMZ?
We are large enough to offer stability and great benefits, yet small enough to recognize you as an individual and not just “another employee.”
Multiple departments from facilities management to engineering allows you to explore different career paths.
The medical devices industry is experiencing explosive growth with no signs of stopping any time soon.
We have completed our 8th expansion which includes amenities such as locker rooms, showers, an expanded cafeteria, and more.
We have a deep bench of knowledgeable pros to help you.
Everything from 401K to top-of-the-line healthcare, life insurance, and more!
What Our Team Members Have to Say
Playlist
Benefits
401(k) Retirement Plan
We will match $0.50 on the dollar up to an 8% contribution. Work with us, retire with us.
Overtime Available
Opportunities to earn overtime hours are available as needed.
Paid Holidays
Enjoy 9 paid holidays off per year.
Paid Time Off (PTO)
PTO starts accruing from the day you start.
Referral Bonus
Employees are eligible to earn a $3,500 referral bonus!
Health Insurance Plans
Enjoy a low employee co-pay with high contributions towards your plan.
Dental Insurance Plans
Yes - we have a great dental plan as well!
Quarterly Bonus
Teams achieving set performance goals receive a quarterly performance bonus.